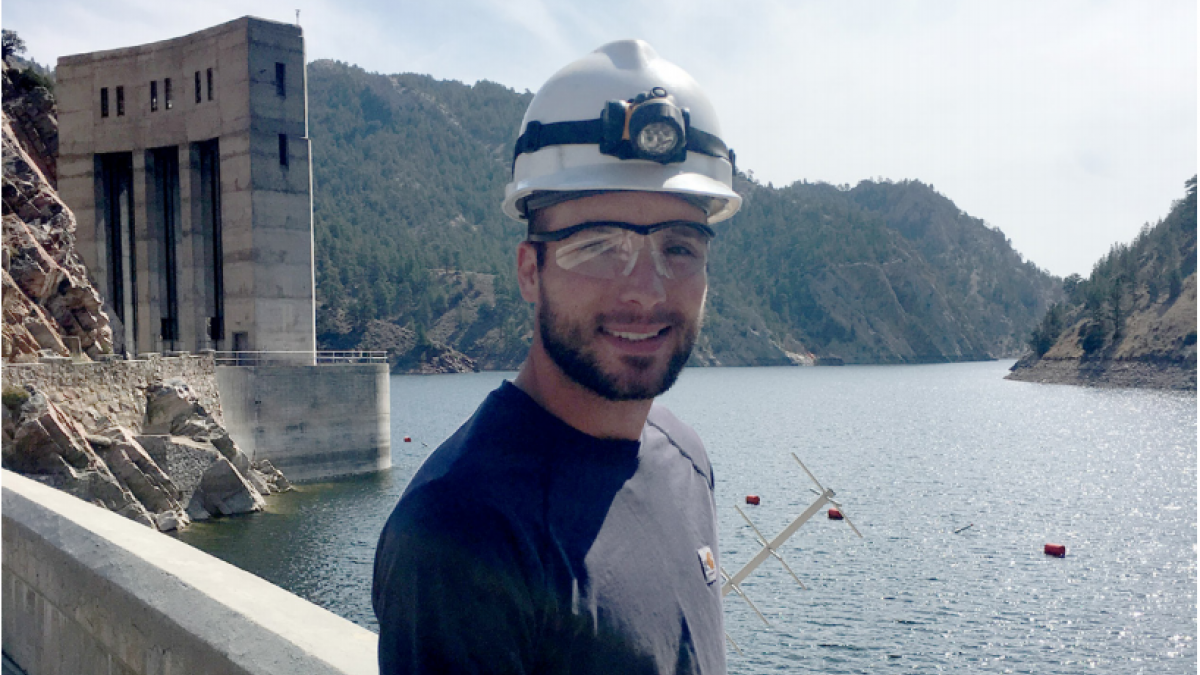
Industrial Equipment Mechanic
Position Overview
Industrial Equipment Mechanics keep DOI running! These highly skilled Mechanics install, maintain, repair, and overhaul equipment and machinery in a variety of environments: industrial treatment plants, pumping plants, shipyards, buildings, hydroelectric power plants, and dams.
This position is represented at the following bureaus
Candidate Description
The ideal candidate can communicate and collaborate with others and apply considerable mechanical skill and strong problem-solving abilities to maintain, troubleshoot and repair equipment, some of which is very specialized. This person can accurately read and interpret blueprints, drawings and instructions and safely operate tools and equipment like cranes, hoists, forklifts, lathes, grinders and soldering irons. Special equipment operator certifications may be required.
Work Environment
Work is physically strenuous and performed both indoors and outdoors in all types of weather. Protective equipment is required and there is potential exposure to noise, vibration, dust, fumes, confined spaces, heights, temperature extremes, and potential injury.
Career Level Requirements
Responsibilities by Level
Entry:
- Assisting higher grade equipment mechanics
- Installing, maintaining, and repairing industrial plant machinery and equipment
Mid:
- Connecting steam lines, couplings, fuel lines, pipes
- Lubricating systems
- Disassembling and assembling components and assemblies
- Locating and repairing or replacing defective parts and components
Journey:
- Inspecting, adjusting, overhauling and maintaining machinery, equipment, and systems
- Lifting and moving machinery, equipment and materials using cranes, hoists, tractors and forklifts
- Disassembling, troubleshooting, repairing and reassembling equipment and systems with complex interrelationships among components
- Making needed repairs by refinishing or fabricating worn or damaged parts and components
- Installing equipment, connecting power sources, performing operational and functional tests and making required adjustments in order to ensure proper operation
- May work individually, as part of a multi-trade work team, and/or guiding and directing helpers and apprentices
Senior:
- Developing or adjusting deadlines, priorities and work plans
- Identifying and obtaining material, equipment, employees and permits required for work projects
- Observing and demonstrating proper work methods
- Answering questions and providing guidance to workers
- Ensuring safety rules are followed
- Monitoring performance and reporting work progress and problems
- Inspecting and approving completed work
Strengths by Level
-
AccountabilityHolds self and others accountable for measurable high-quality, timely, and cost-effective results. Determines objectives, sets priorities, and delegates work. Accepts responsibility for mistakes. Complies with established control systems and rules.Show Tool TipEntry 1-2Mid 3-4Journey 5-6Senior 7-10
-
Attention to DetailIs thorough when performing work and conscientious about attending to detail.Show Tool TipEntry 1-2Mid 3-4Journey 5-6Senior 7-10
-
Interpersonal SkillsTreats others with courtesy, sensitivity, and respect. Considers and responds appropriately to the needs and feelings of different people in different situations.Show Tool TipEntry 1-2Mid 3-4Journey 5-6Senior 7-10
-
Physical Strength and AgilityAbility to bend, lift, climb, stand, and walk for long periods of time; ability to perform moderately heavy laboring work.Show Tool TipEntry 1-2Mid 3-4Journey 5-6Senior 7-10
-
Problem SolvingIdentifies problems; determines accuracy and relevance of information; uses sound judgment to generate and evaluate alternatives, and to make recommendations.Show Tool TipEntry 1-2Mid 3-4Journey 5-6Senior 7-10
-
Self-ManagementSets well-defined and realistic personal goals; displays a high level of initiative, effort, and commitment towards completing assignments in a timely manner; works with minimal supervision; is motivated to achieve; demonstrates responsible behavior.Show Tool TipEntry 1-2Mid 3-4Journey 5-6Senior 7-10
-
StaminaExerts oneself physically over long periods of time without tiring (which may include performing repetitive tasks such as data entry or coding).Show Tool TipEntry 1-2Mid 3-4Journey 5-6Senior 7-10
-
Teaching OthersHelps others learn through formal or informal methods; identifies training needs; provides constructive feedback; coaches others on how to perform tasks; acts as a mentor.Show Tool TipEntry 1-2Mid 3-4Journey 5-6Senior 7-10
-
TeamworkEncourages and facilitates cooperation, pride, trust, and group identity; fosters commitment and team spirit; works with others to achieve goals.Show Tool TipEntry 1-2Mid 3-4Journey 5-6Senior 7-10
-
Technical CompetenceUses knowledge that is acquired through formal training or extensive on-the-job experience to perform one's job; works with, understands, and evaluates technical information related to the job; advises others on technical issues.Show Tool TipEntry 1-2Mid 3-4Journey 5-6Senior 7-10
Common Pathways
Candidates who made this career change most commonly held these occupations...
High Voltage Electrician
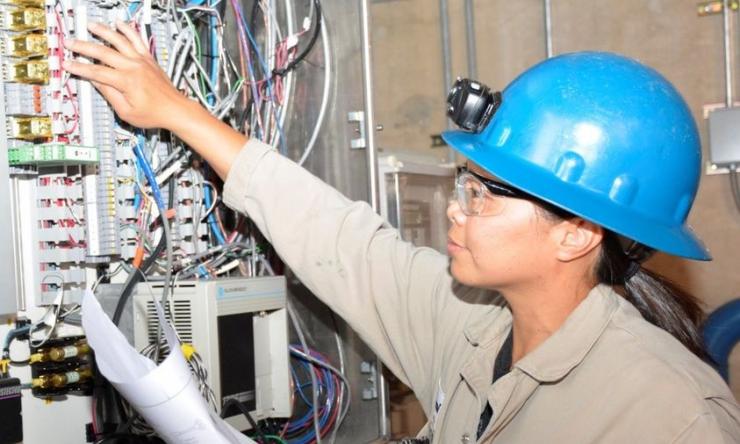
Utility Systems Repairing - Operating
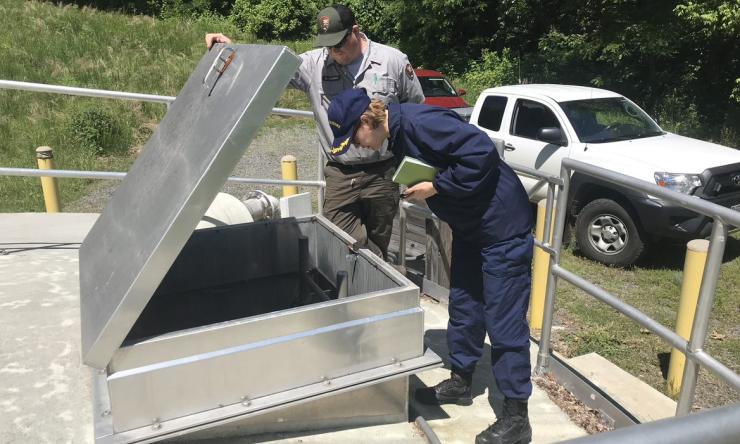
Electric Power Controller
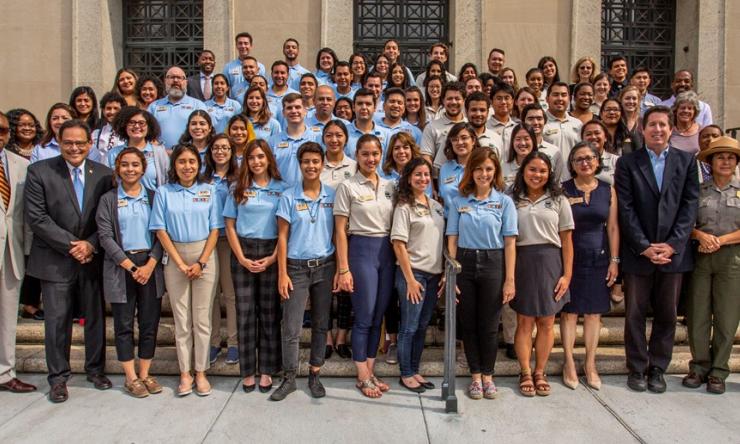
- 0346 - Logistics Management
- 0802 - Engineering Technician
- 3359 - Instrument Mechanic
- 5026 - Pest Controlling
- 5803 - Heavy Mobile Equipment Mechanic